High Speed Pick, Inspection and Packaging Machine
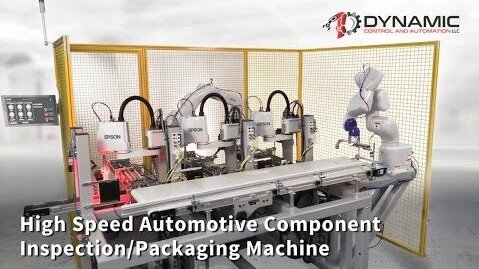
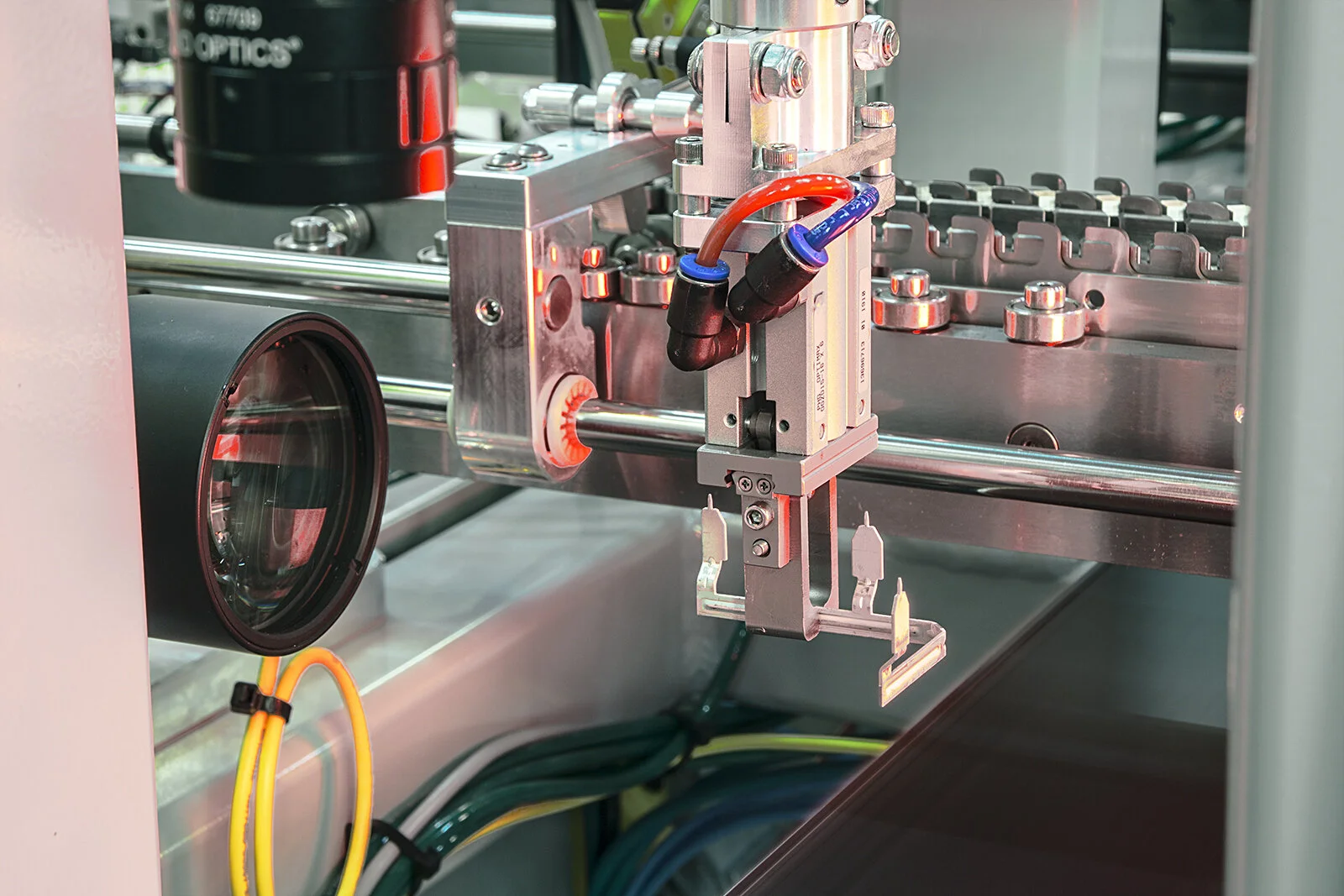


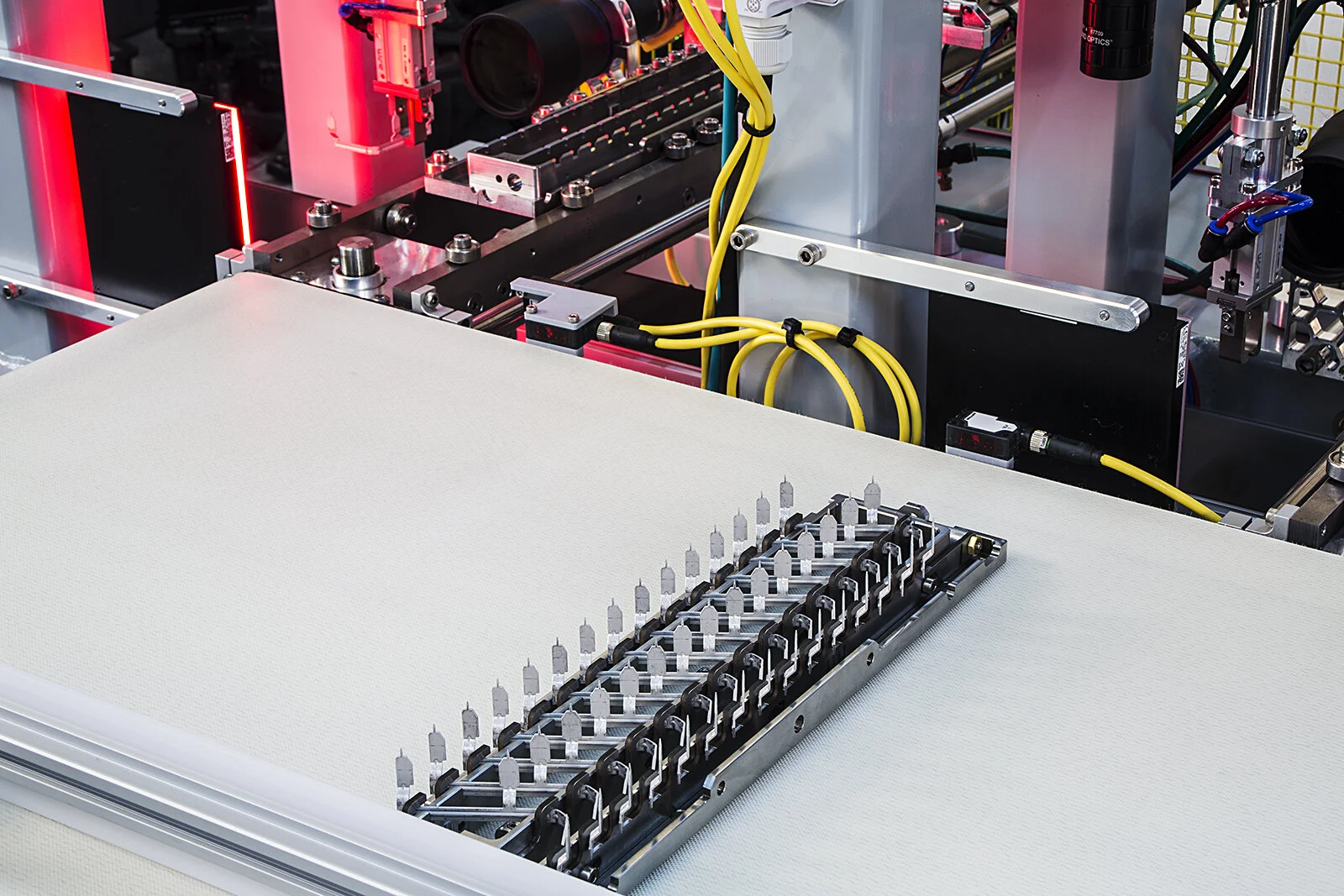
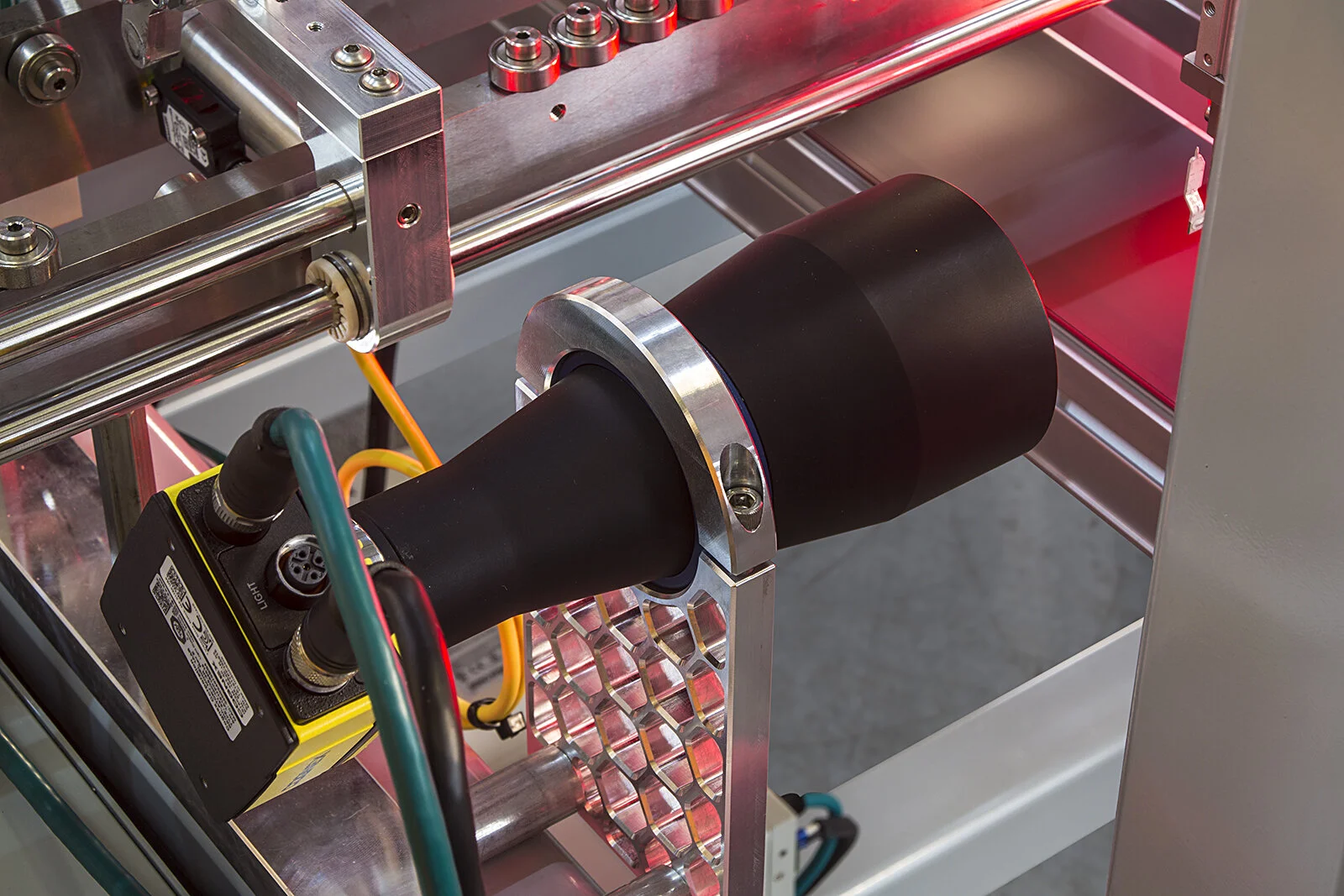



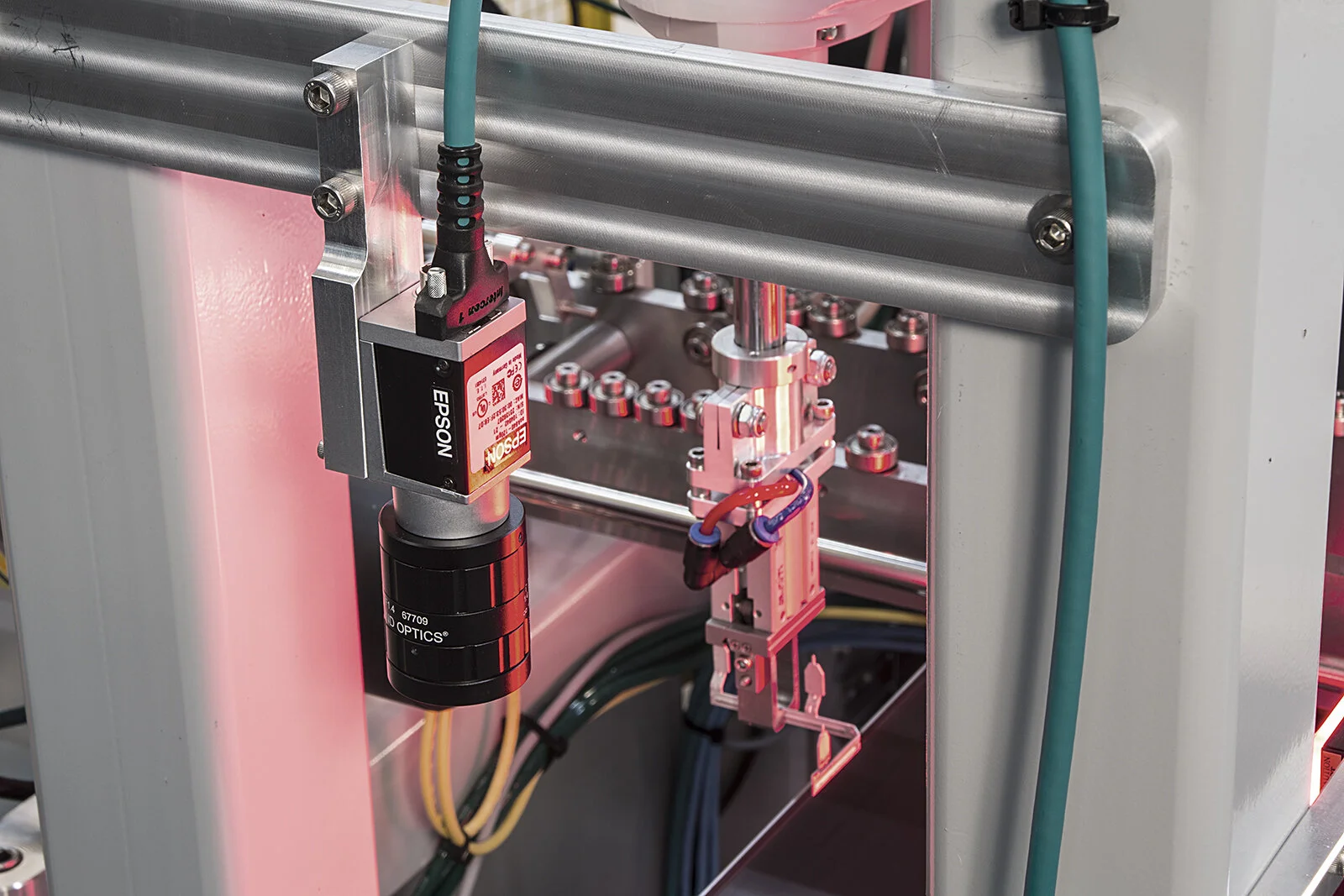


Project Description: This system is one module of a fully automated system which performs precise 3-D visual inspections, ultrasonic wash, and final packaging of stamped steel automotive antennas.
Operation: This “Inspection Module” intercepts moving antennas as they exit a multi-stage stamping/forming press, performs the visual inspection to micron-level accuracy, then loads the antennas into precision custom “cartridges”. These cartridges are used to transport and protect the antennas during downstream processes (automated ultrasonic wash and automated packaging). These cartridges are automatically circulated throughout the overall system via robots, conveyors and a unique “shuttle” system used to rapidly exchange cartridges for each of the three robots performing the inspection and placement operations.
Mechanical Architecture: The inspection module is comprised of a core frame, with two bolt-on external sub-weldments to mount 6axis Epson VT6L robots. This was necessary to reduce the overall size for transportation and installation. The primary conveyor, shuttle systems, sensors, and 3 Epson SCARA robots all mount to the primary frame.
Motion:
· Inspection and Antenna Placement: 3x Epson G3 SCARA robots
· Cartridge Placement: 2x Epson 6 axis robots
· Cartridge Load/Eject: Pneumatic
· Conveyors: Electric with encoder tracking
· Sensors: Various – through beam, ultrasonic, proximity inductive.
Vision: 3x Cognex 7000 series cameras with collimated back lighting for inspection. Epson vision for conveyor tracking.
Safety: Full perimeter 80/20 safety cage with safety interlocked hinged door.
Primary Challenges and Solutions:
1. Processing speed: The rate of antenna production required three robots, each working at or near its maximum speed. More robots could not be accommodated due to floor space limitations.
Solution: A compact series “waterfall” design with a single conveyor whereby each robot would be presented with a continuous input comprised of what the upstream robots simply couldn’t process.
2. Cartridge change out for robots: Due to the high speed of incoming product, full cartridges had to be exchanged for empty units within 1.5 seconds.
Solution: Custom cartridges that are able to protect and locate the antennas during rapid ejection, combined with a dedicated fast-acting pneumatic shuttle system to exchange cartridges for each robot.
3. Visual Inspection: The rigorous inspection requirements demanded innovative use of Cognex vision tools, lensing, and lighting.
Solution: The SCARA End-of-Arm tooling was designed to allow very precise repeatability during retrieval and inspection such that the inspection algorithm could be optimized. Each antenna was reliably inspected in less than 50mS.
4. Installation: Between project kickoff and installation the customer had made physical changes in their plant that necessitated partial disassembly of the system to allow movement through the plant to the installation site.
Solution: Added access assessment to Dynamic’s pre-installation checklist.