Packaging Machine Project
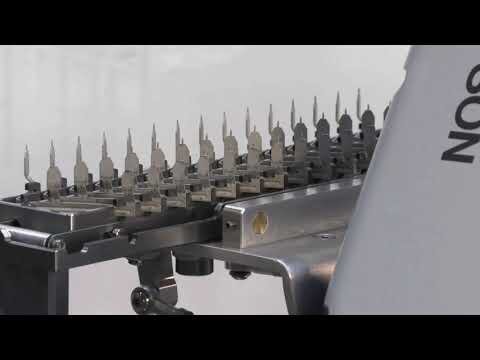



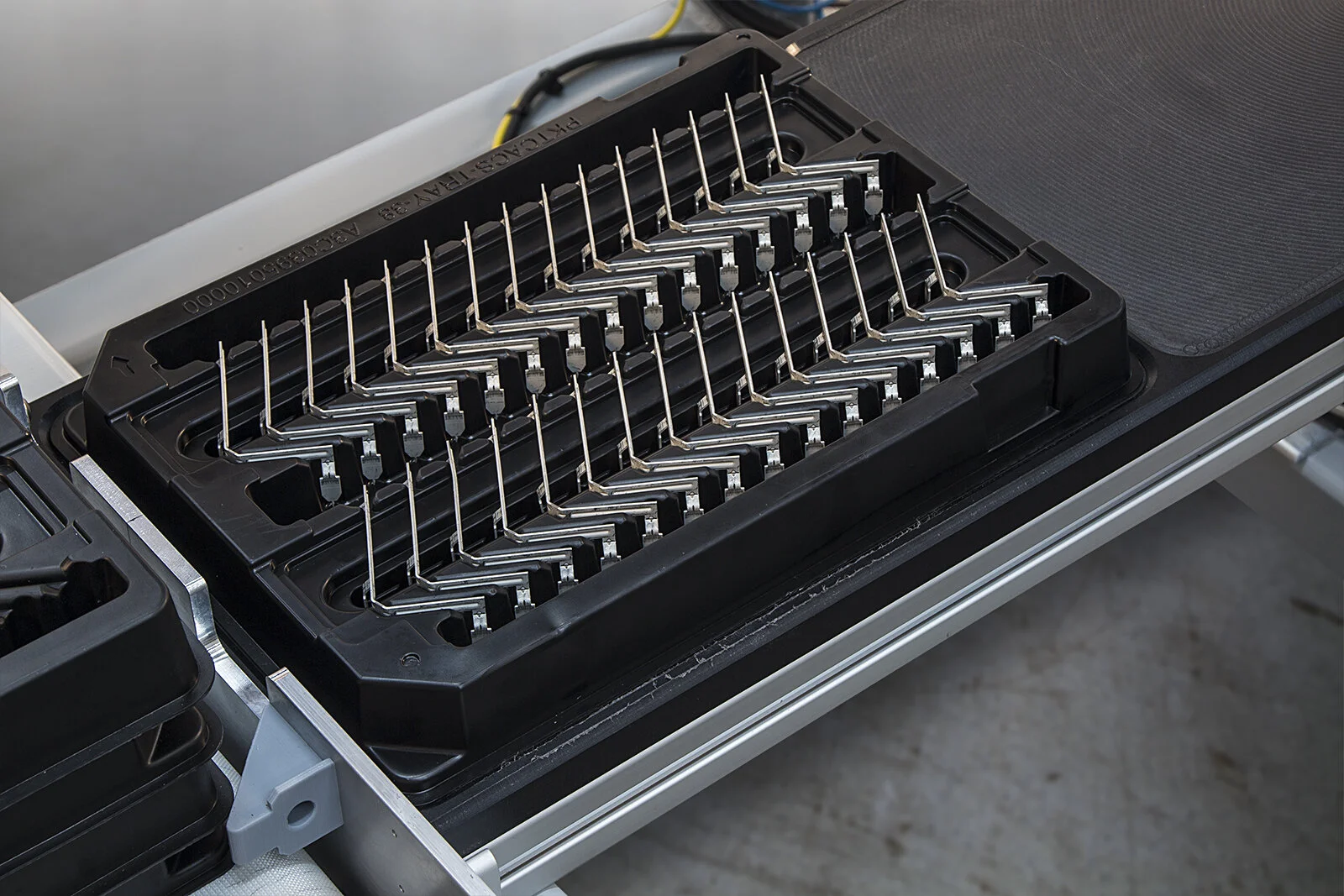




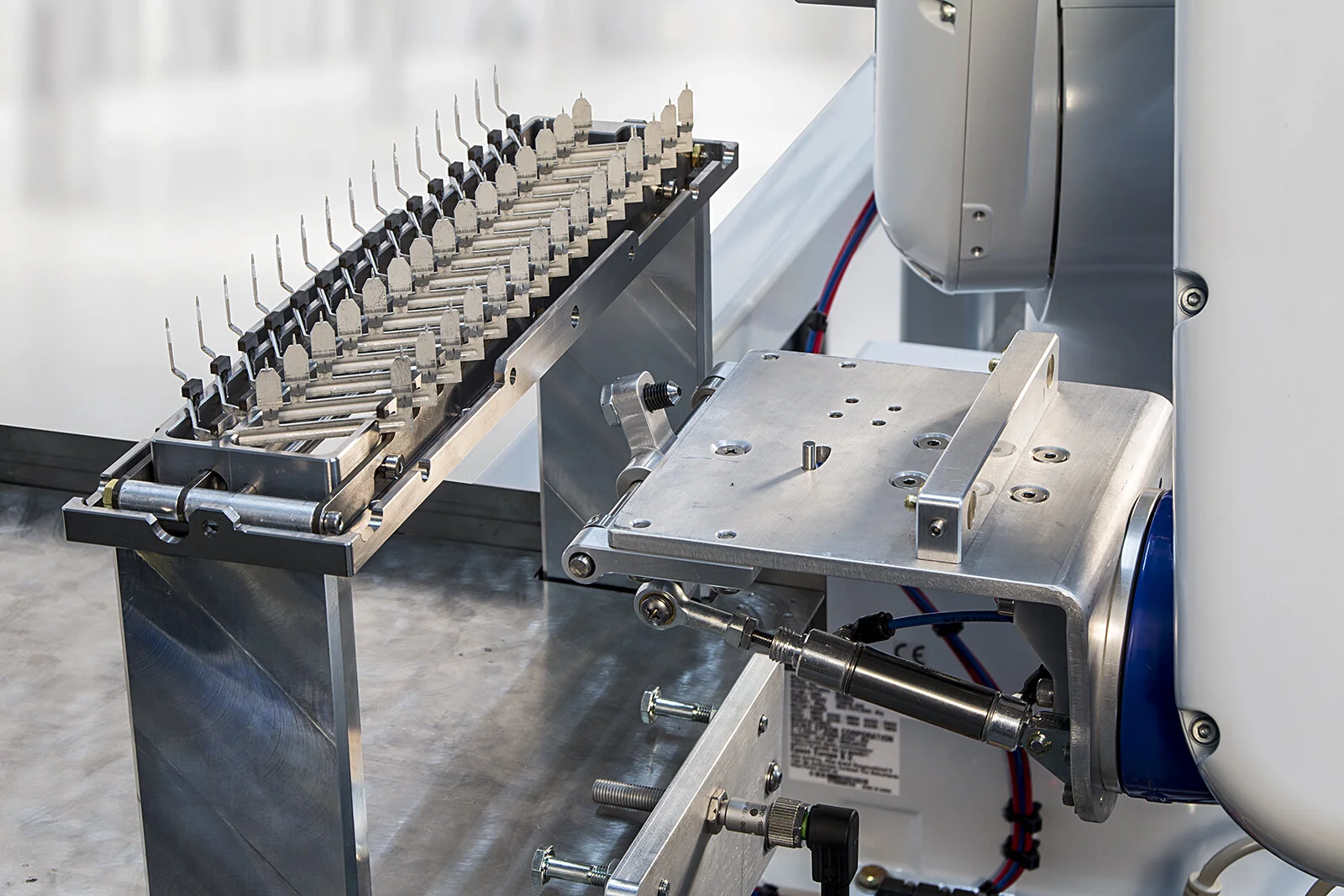


Operation: This “Packaging Module” retrieves custom cartridges (loaded with antennae) from an ultrasonic wash unit. The cartridges are staged in a precision lift station for pickup by one of the first of two Epson 6 axis robots.
Robot 1: The dock raises the cartridge so that the End-of-Arm tooling on the Epson robot can grip it on its underside. Once the cartridge is captured by the robot, it is flipped and precisely positioned over a packaging tray where all of the antennae are dropped simultaneously. The cartridge is then placed onto a de-lift station, where it is ejected onto a conveyor to be recirculated.
Robot 2: This robot is dedicated to stacking and destacking shipment trays for the antenna. Operators load an input conveyor with stacks of trays, which are then advanced as needed into a stationary transfer station. Robot 2 picks trays from this station for placement on one of two loading stations. When a tray is full, Robot 2 transfers the full tray to a stack on the output conveyor. Operators retrieve stacks of full trays from the output conveyor for shrink wrap and boxing.
Mechanical Architecture: The packaging module is comprised of a single powder-coated a core frame weldment. Infeed and outfeed conveyors are provided for stacks of shipping trays for the antennae.
Motion:
Cartridge Placement: 2ea Epson 6 axis robots with custom End-of-Arm tooling (EOAT).
Conveyors: Automated electric, via main processor control.
Sensors: Through beam, ultrasonic, proximity capacitive.
Vision: None
Safety: Partial perimeter 80/20 safety cage with safety interlocked hinged door. Openings provided for operator access to load/unload trays.
Primary Challenges and Solutions:
1. Tray Stack/De-Stack: The custom shipping trays were difficult to stack with sufficient precision to allow automated handling.
Solution: A custom End-of-Arm tool and custom docking guides were developed to straighten and align the trays during transit on the infeed conveyor.
2. Antenna drop Accuracy: The antennas had to be dropped in “tips-down” configuration from above the shipping trays with 100% reliability and without the benefit of vision guidance.
Solution: The same cartridges used to transport and protect the antennae during wash were also provided with retention mechanisms that allowed the antennae to drop free of the cartridge when inverted. It was necessary to drop the antennae without tilting/tipping the antenna out of the horizontal plane to prevent bounce during the gravity drop into the trays.