Small Case Erecting and Packaging Machine
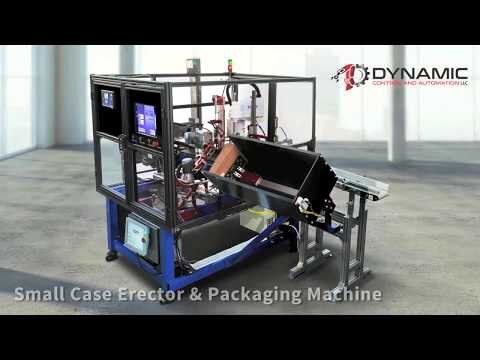
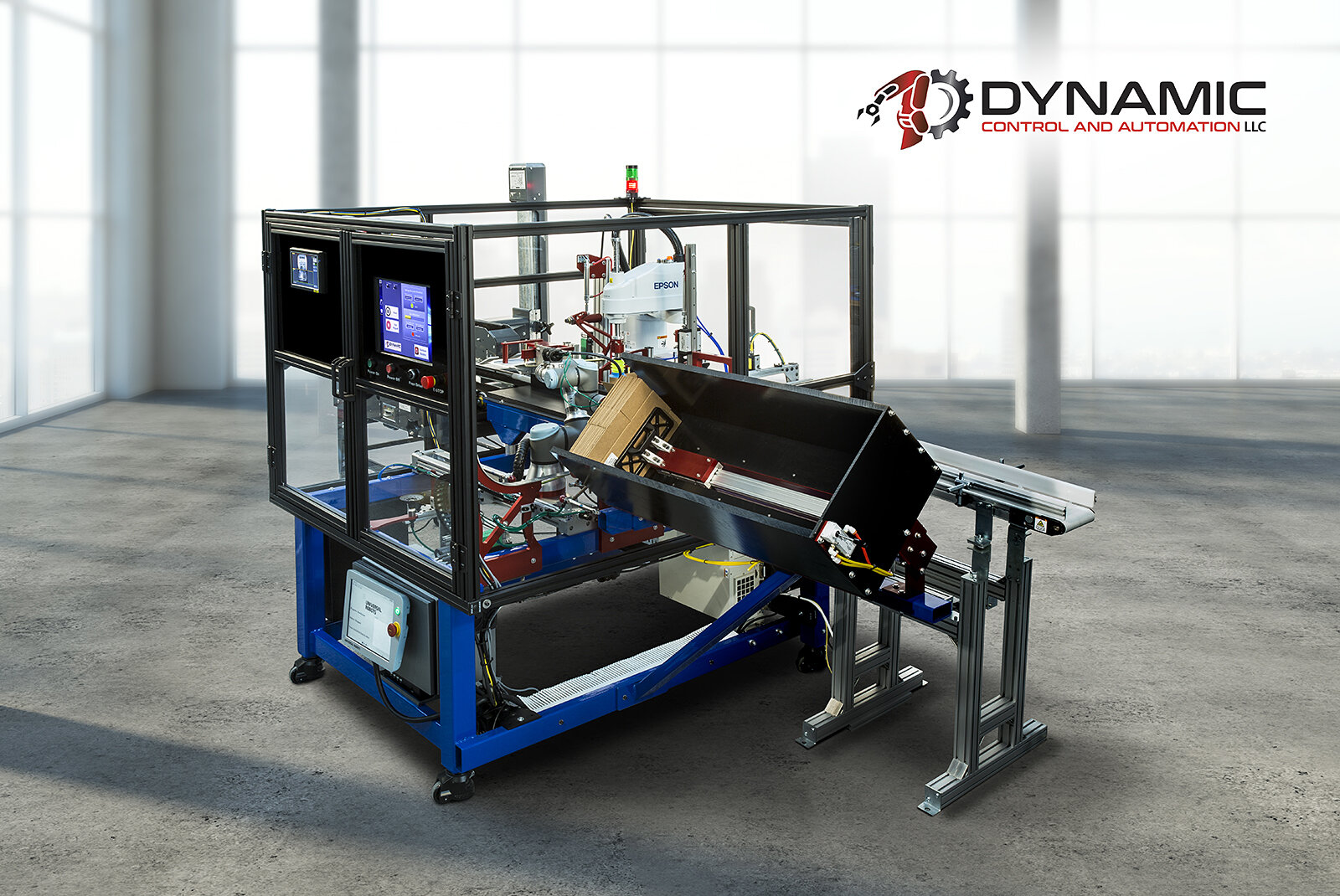
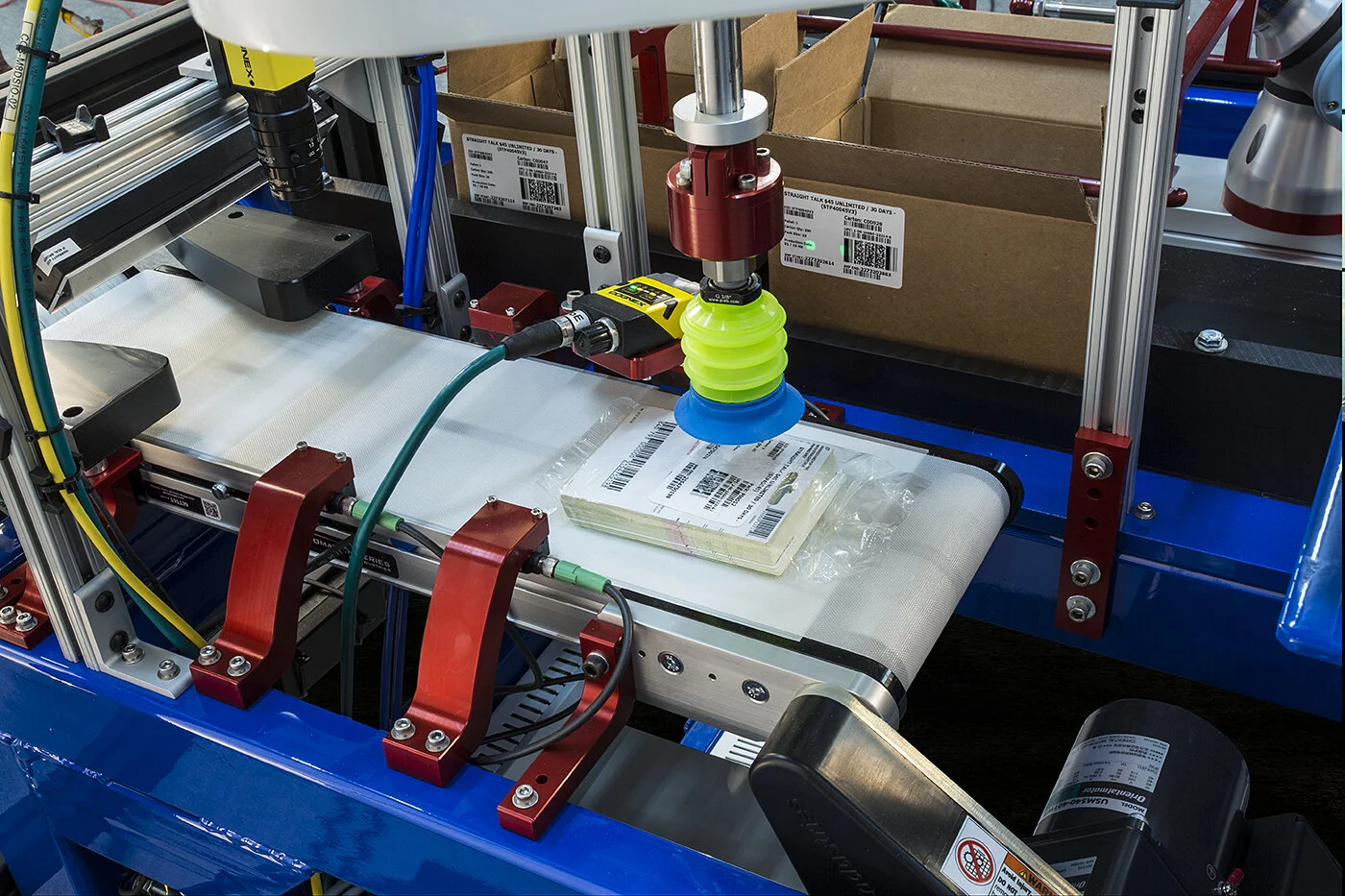
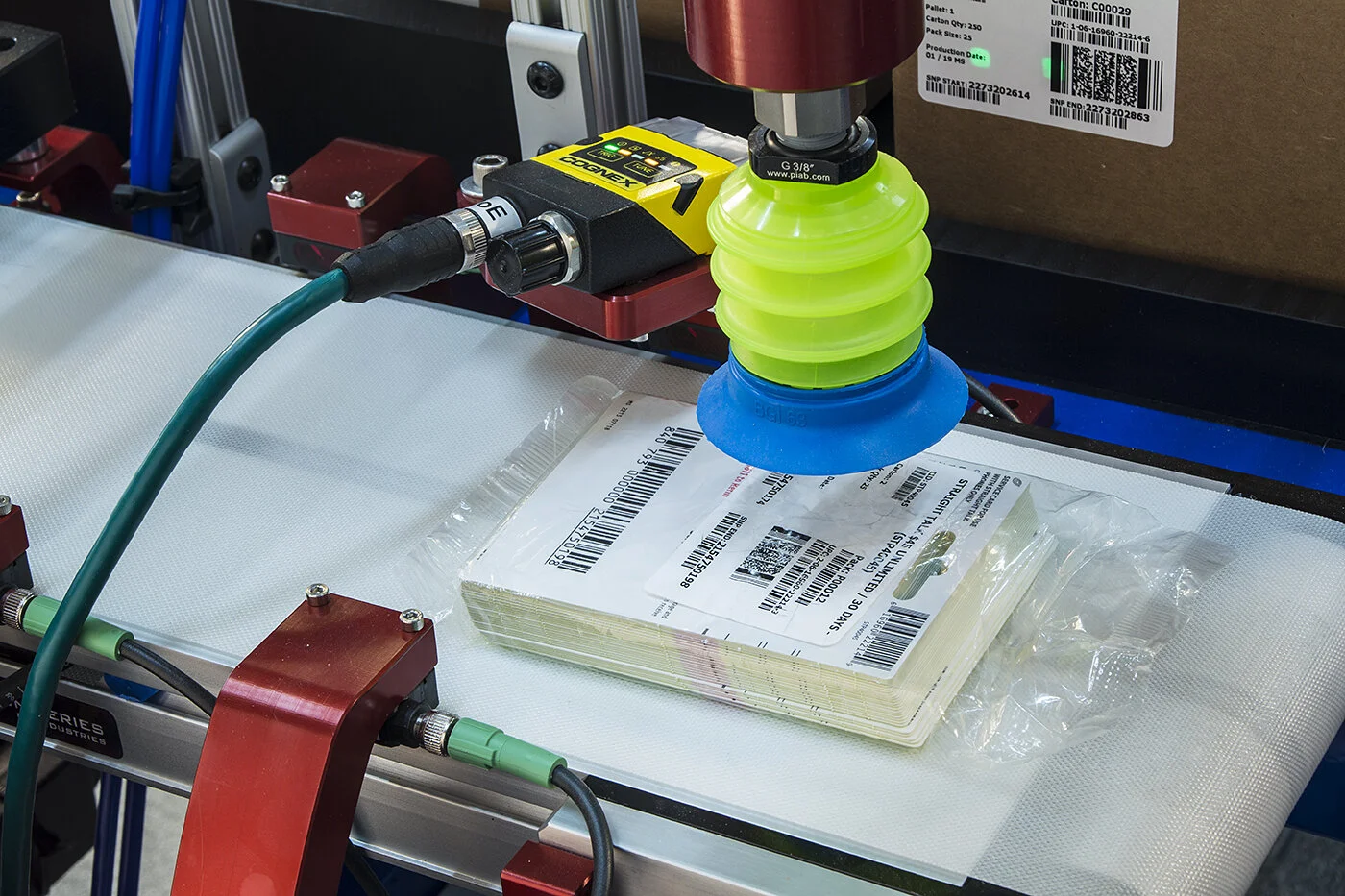
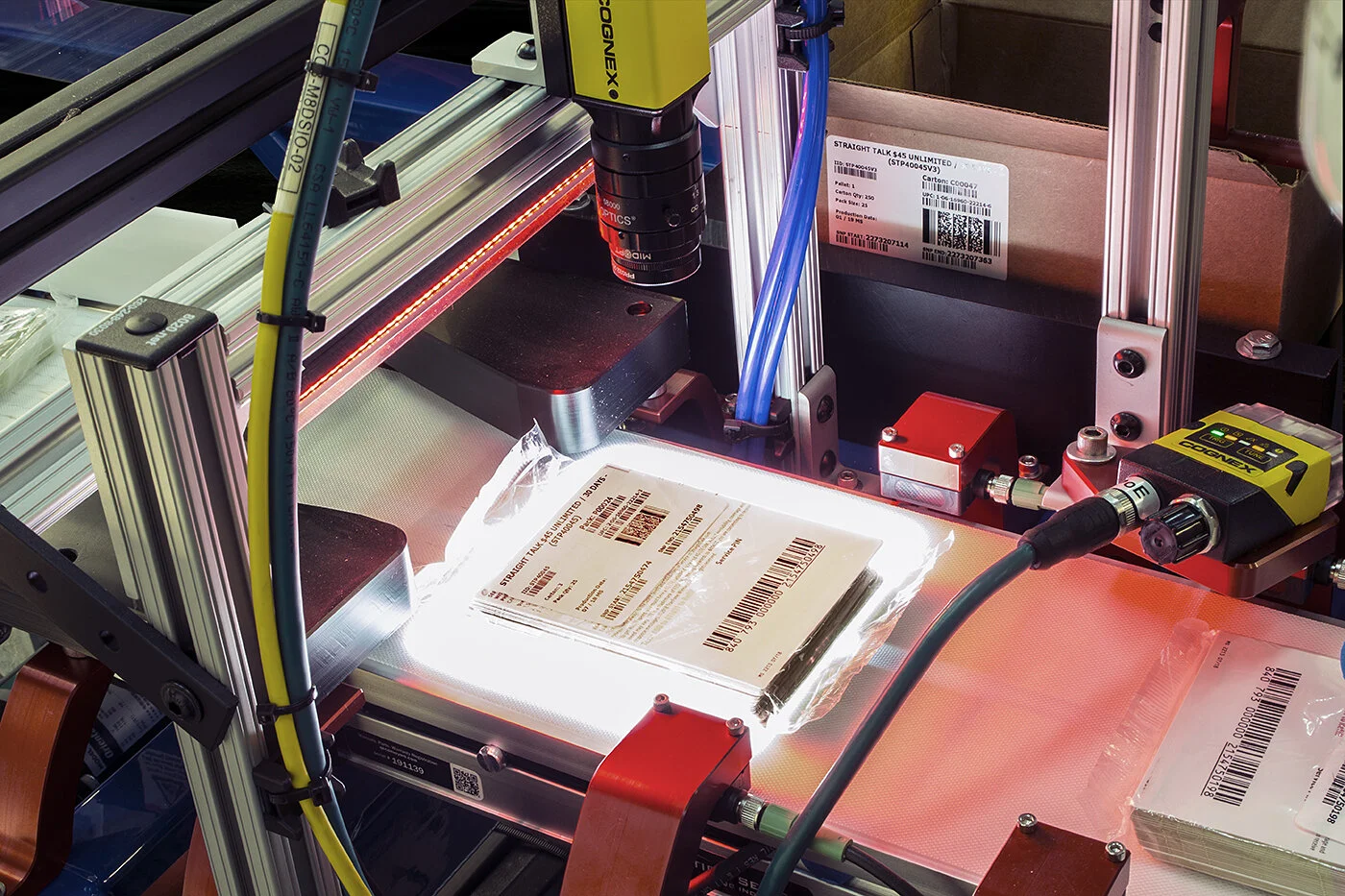
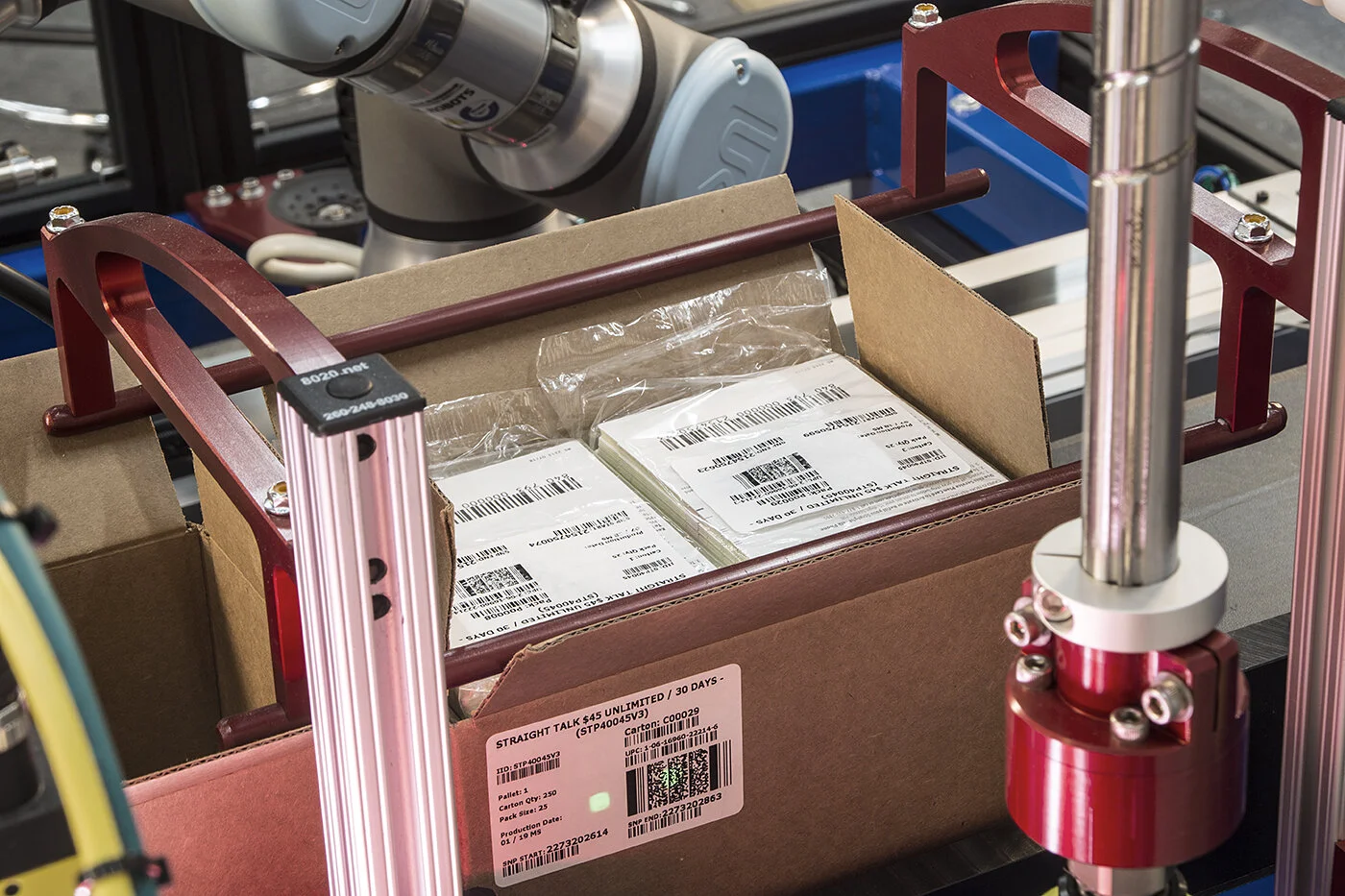
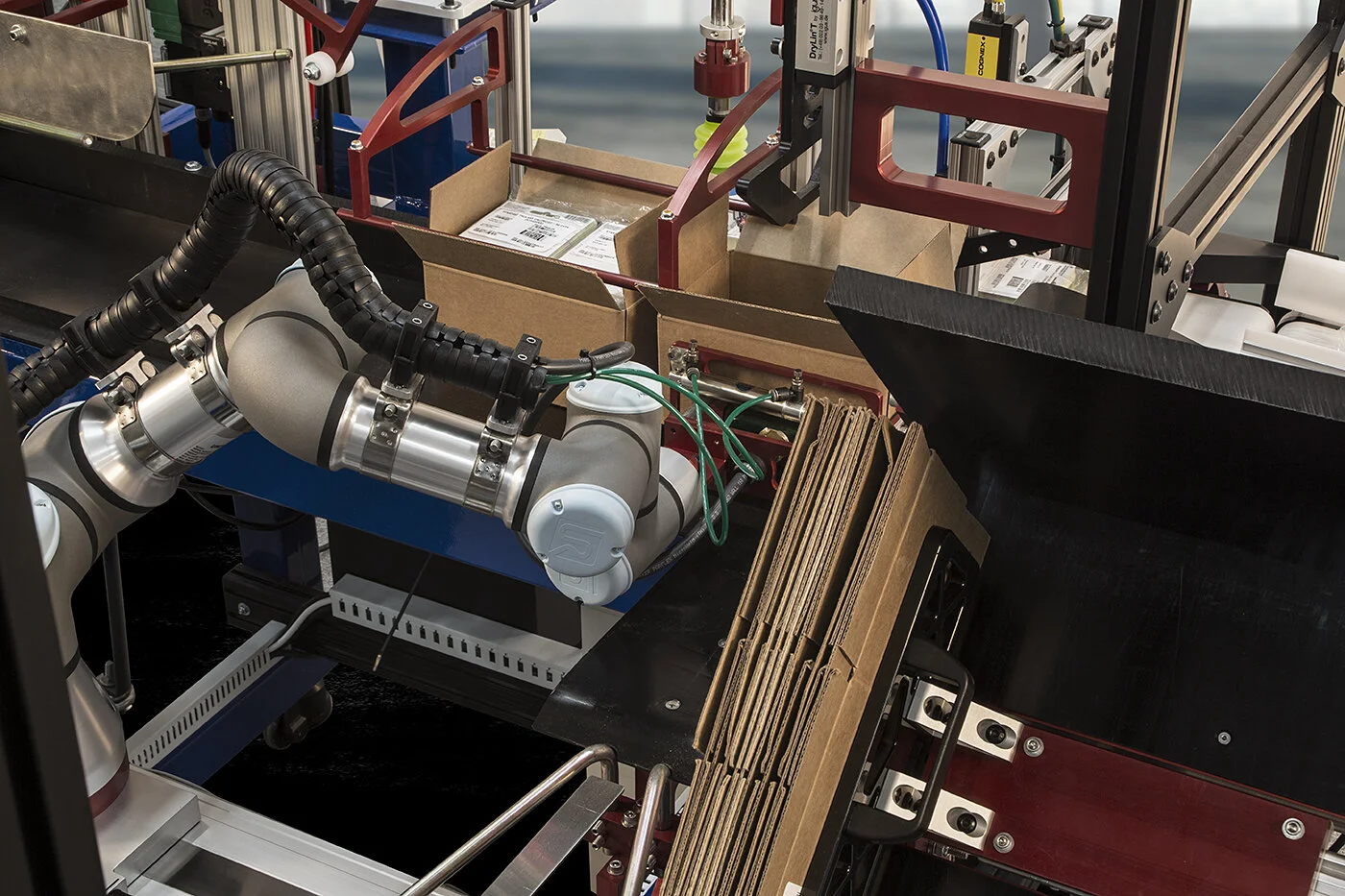
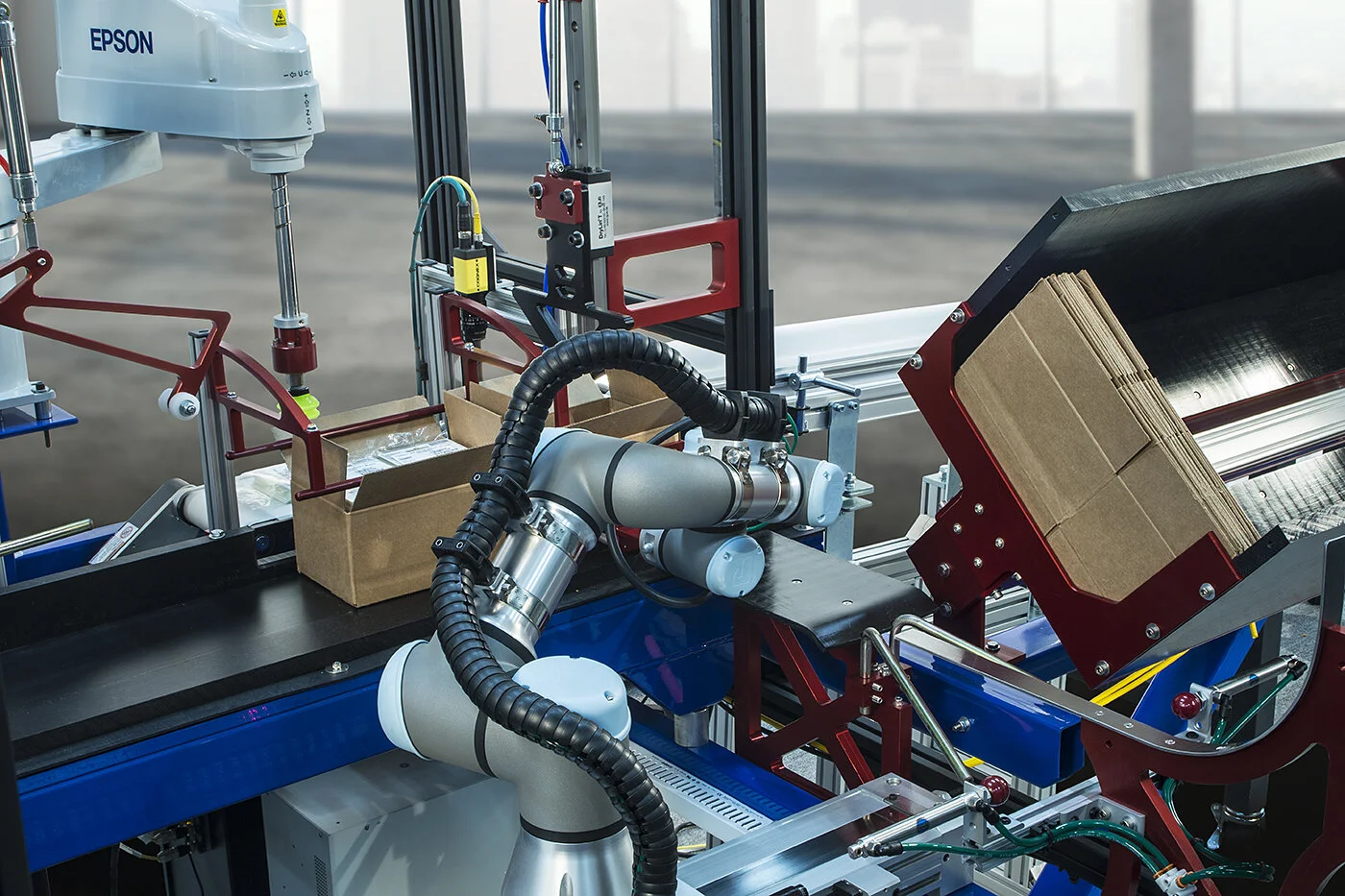
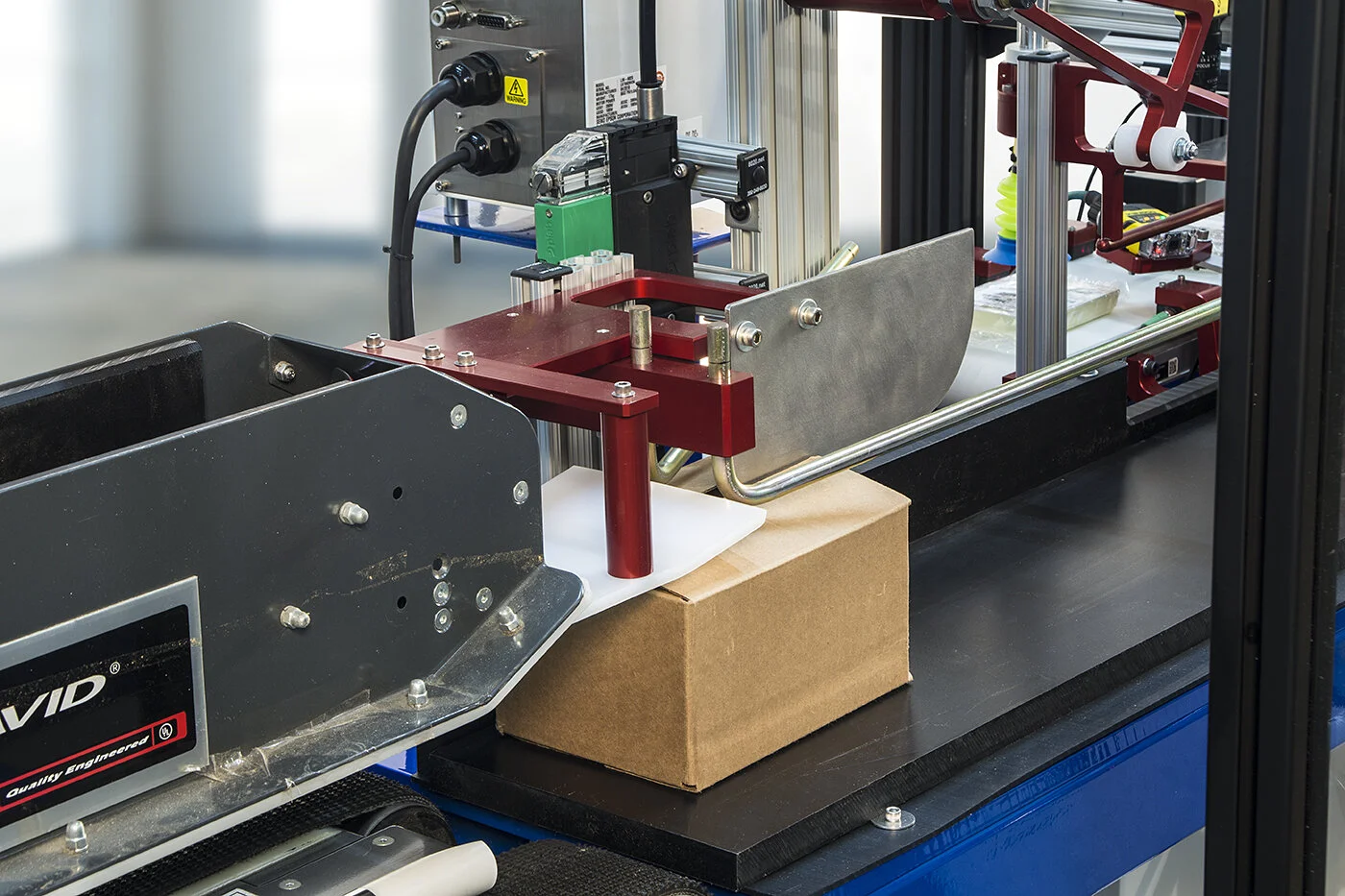

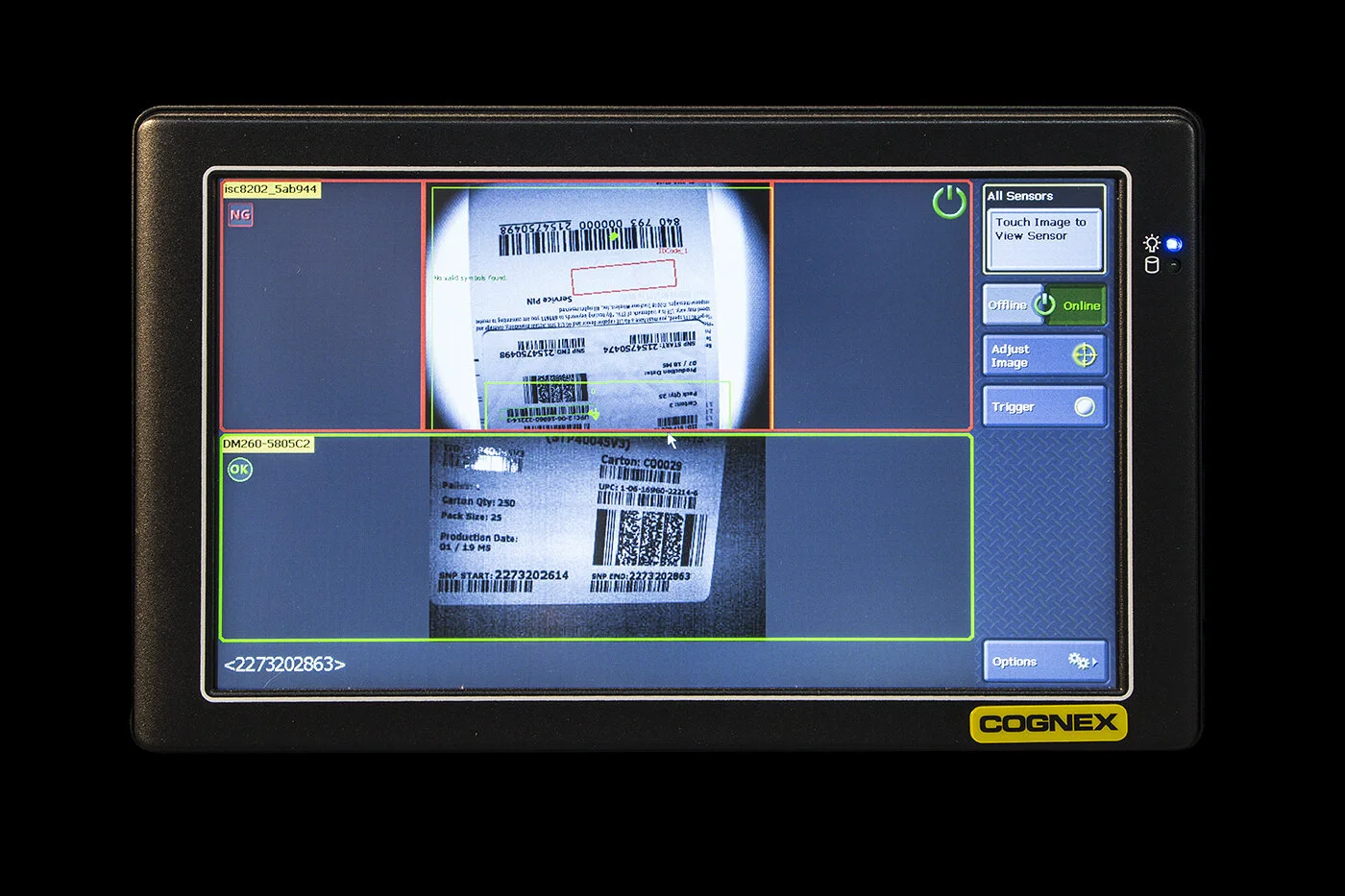
Project Description: This system is a fully automated self-contained case erecting and packaging system.
Operation: This case erecting/packaging system operates with two asynchronous subsystems.
Robot 1 - Case Erecting: Cases are erected automatically by a UR3 6 axis robot utilizing a custom End-of-Arm tool. These cases are retrieved from a custom magazine by the robot, erected, then moved to a staging station. The robot waits at the staging station with the case until given the signal to advance by the Case Filling robot.
Robot 2- Case Filling: This robot is dedicated to moving product from an automated inspection station where good/bad determinations are made by dedicated barcode readers. A second barcode reader confirms a barcode on the case itself. If the barcode readers confirm a match, the Epson Scara robot retrieves the package (using vacuum suction cups) and moves it into the case.
When a case has been filled, it is pushed forward by the 6 axis robot (which is simultaneously moving the next empty case into position). The Robot then translates, and moves the full case out of the machine and onto a case sealer (the product is subsequently automatically palletized on a Dynamic Control and Automation robotic palletizer).
Mechanical Architecture: The Card Packaging System is constructed using a two-piece powder-coated steel weldment.
Motion:
Product Casing: 1ea Epson Scara robot with custom End-of-Arm tooling (EOAT).
Case Erecting: 1ea UR3 6 Axis collaborative robot with custom End-of-Arm tooling.
Sensors: Through beam, ultrasonic, proximity capacitive.
Vision: Cognex 8000 series and Cognex Dataman
Safety: Full perimeter 80/20 safety cage with safety interlocked hinged door for maintenance. Openings provided for operator access to load cases.
Primary Challenges and Solutions:
1. Case Erecting: The small size of the cases and poor creasing/consistency prevented the use of standard “Off the Shelf” End-of-Arm tooling.
Solution: A custom End-of-Arm tool and custom case erector were designed for this project. A custom “4th flap” closer for a “Little David” case sealer was also designed to complete the automated process.
2. Overwrapped Package Movement: The overwrapped cards were highly variable in terms of thickness, entrapped air, and conformation to the interior product profile.
Solution: Custom gates, guides, vision algorithms, and sensors were employed to ensure accurate pickup and placement of the product into cases.